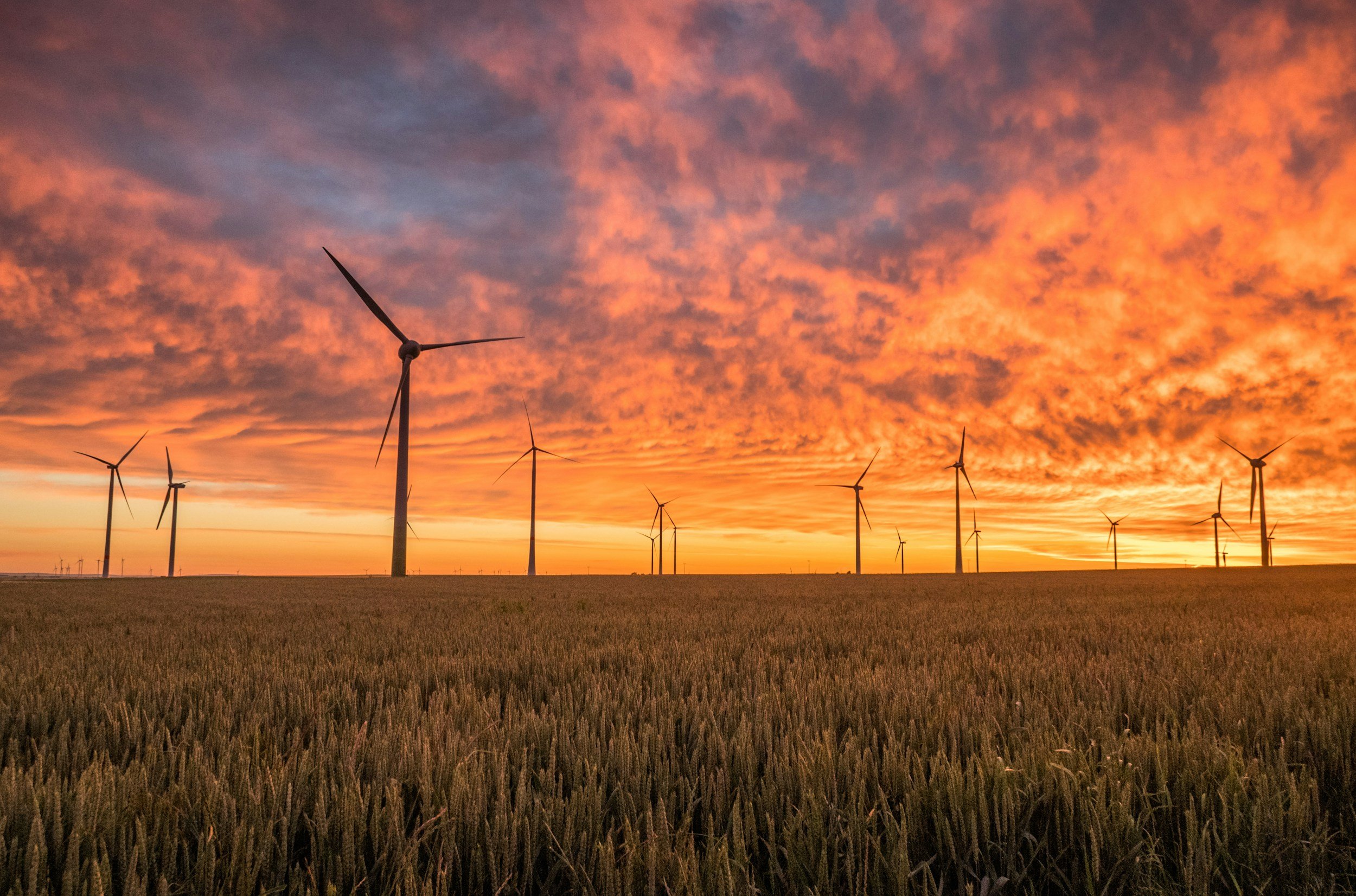
Specialising in Statutory Compliance, Inspection & Maintenance
We have a formal supply chain Partnership in place with all major towerhoist manufacturers and hold approved service centre status for specific brands, with the ability to provide a range of training and component and on site services on mainstream brands such as Skyman, Avanti, Goracon and Powerclimber.
We have a full stockholding of standard parts in our Glasgow Warehouse inclusive of Hoists and Brakes. Our technicians attend site with all common spares and faults are fixed at the scheduled maintenance and inspection to avoid the need for a revisit.
Skyform Wind’s approach to compliance, inspection and maintenance is focused on ensuring that wind turbine downtime is minimised.
To achieve this:
We aim for 100% compliance through Statutory Inspections.
We have a real-time wind turbine management IT system.
We have a unique database system for managing all access systems in any windfarm.
We have dedicated squads of engineers that are fully trained and competent to complete all service, inspection & repairs.
Our technicians go through a comprehensive training package which covers the installation, scope of inspections, servicing and lift and crane training.
We develop the skills of our engineers enabling them to access and support any windfarm in the United Kingdom & Europe.
We have a fully equipped workshop to provide repairs to the Skyman hoist and safety brake quickly and efficiently without having to send equipment to Belgium to repair.
We provide certification of thorough examination for all equipment that is serviced or repaired in the workshop.
We provide full support on training via our in-house training centre.
“…on all the projects I have found Skyform’s Management to be professional and first class in providing the required services and experienced personnel on site in a timely manner”
Training & Competency
Competency is demonstrated through our corporate and people accreditation and training accomplishments.
In 2019 we became Full members of LEEA and are the first wind services provider in our field to achieve this level of membership. This has been achieved through continual investment and dedication in the resources of the company and developing our staff training to the high standard required by LEEA and by meeting the required corporate competency levels.
We believe that the development of the skill of our workforce is of key importance to delivery of our works and attaining customer satisfaction. We understand the value of product specific training but moreover understand the need to train beyond the basic level of understanding that these courses are designed to give. We develop further understanding of the products we work with through our dedicated training centre and hands on job experience and mentoring.
Skyform provide mentoring and support to technicians in the field and carries out on the job assessments to ensure that they understand the job and are performing to the required standard and that future development needs are identified.
The majority of our systems and inspection processes are tailored specifically to meet client expectations. We have a developed knowledge of the items of plant and equipment that we inspect and maintain and are open to continually learning and developing our knowledge further.
Shared Vision
Skyform Wind supports our clients' mission to develop and enable energy systems that are green, independent and economically viable.
Skyform Wind adopts the guiding principles:
SAFETY: Protecting our personnel, clients and contractors
PASSION: Always exceeding our customer's expectations
EXCELLENCE: Provision of high quality services and support
COMPETENCE: Continual development and training of personnel
INDEPENDENCE: Inspection services compliant with legislation and UKAS
COMMITMENT: Improving our services, personnel and systems
We operate with integrity and care, seeking to have a positive impact wherever we work, both in the short and long term. This not only applies to our own business conduct but extends to our suppliers.
Providing Our Clients with Real Time Information
Skyform Wind uses an online Asset Management and Inspection database to provide real time information on all turbines, including which assets are due for service.
The Skyform Tablet is used in combination with the bespoke Database Application which has been developed for Skyform Wind.
Reports are synchronised straight from the tablet back to the office.
The database contains all asset data and supports full traceability of all service and maintenance works.
The tablet is used by technicians to take photographs, follow multiple assets within the turbine and create Inspection Reports. Automated reports can be sent to Site Managers to provide a breakdown of work completed on the visit. Automated emails can also be sent to clients informing them of scheduled 6 month or 12-month services.
“Skyform is a loyal and reliable business partner of Skyman having worked together for over 20 years. If you were to ask Skyman who is the number 1 name to call in the UK for installing, commissioning, maintaining, inspecting and troubleshooting of our suspended powered access equipment, we would say Skyform”
Certifications and Accreditations
Skyform hold several certifications, accreditations, professional memberships and trade associations to ensure that we are continually operating to the highest industry and quality standards.
Skyform Projects and Work Experience
Click here to learn more about Skyform’s work history and who we work with
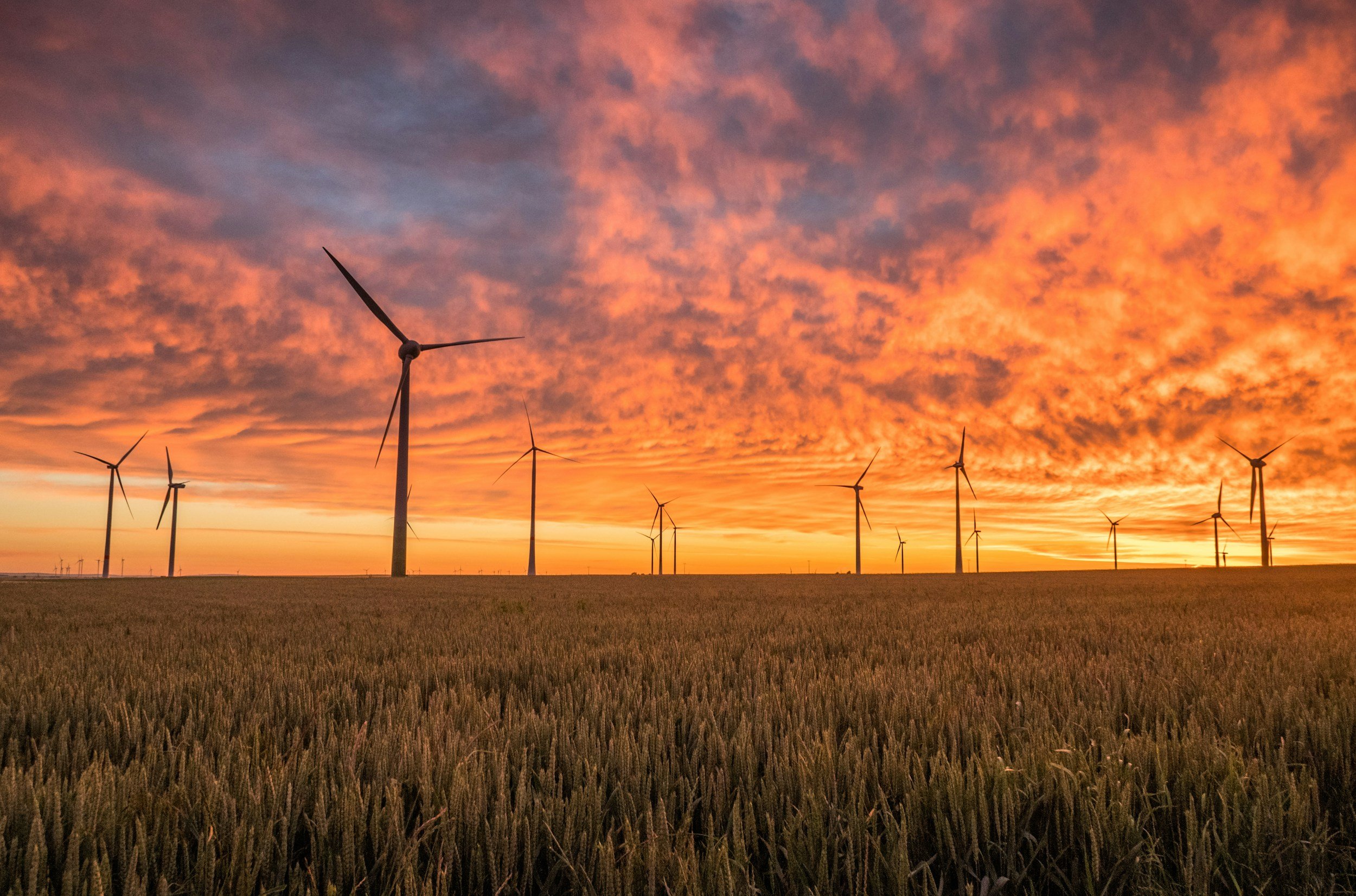